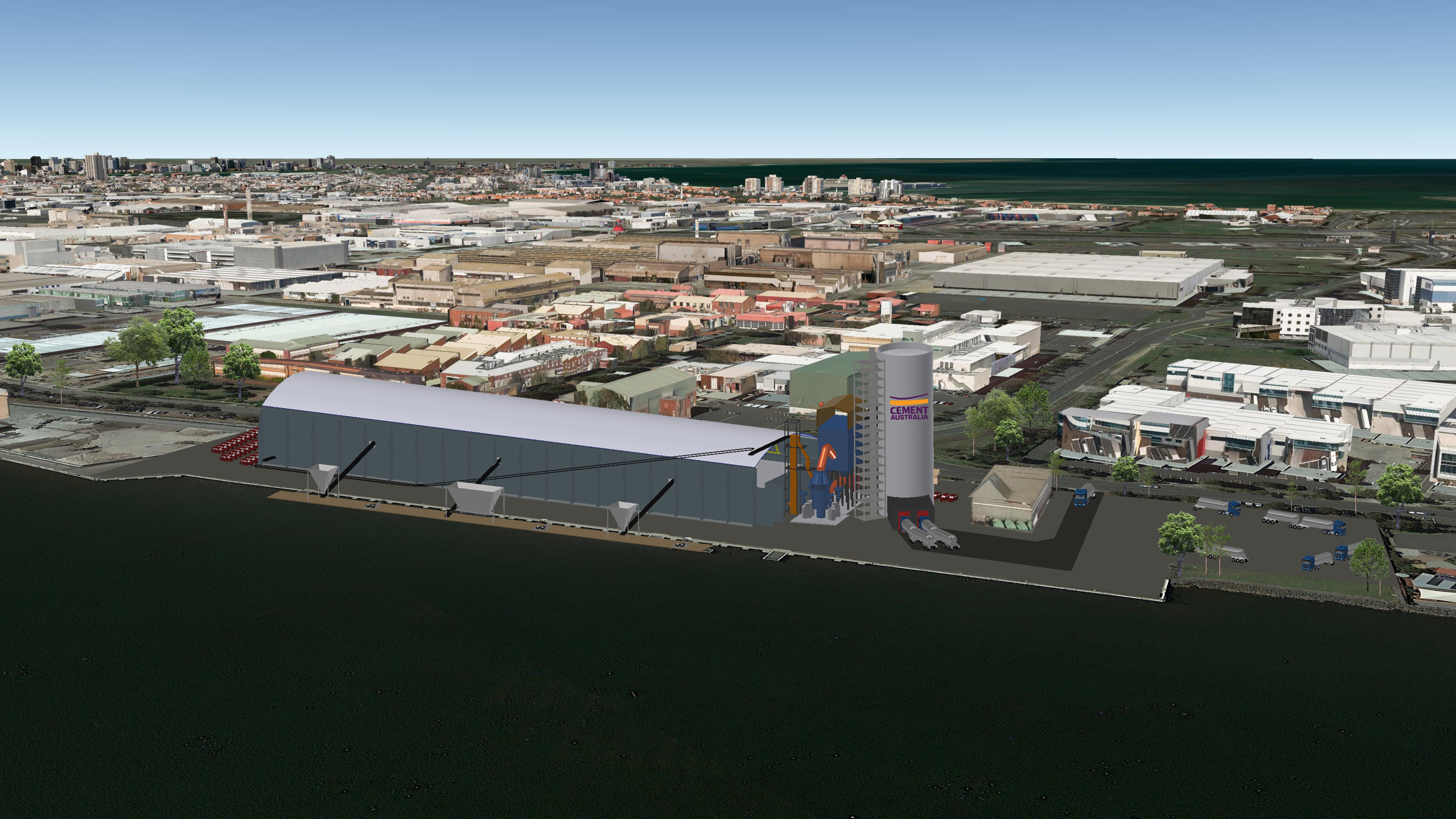
Cement Australia Port Melbourne Slag Grinding Facility
Cement Australia is preparing a Works Approval application to the Environment Protection Authority (EPA), to construct and operate a Slag Grinding Facility at 465 Lorimer Street Port Melbourne.
As part of the Works Approval process, Cement Australia is consulting with relevant stakeholders prior to lodgement of an application for Works Approval with the EPA. The consultation process will help Cement Australia to understand stakeholder concerns and address these concerns.
The Site is located at 465 Lorimer St, Port Melbourne, and occupies parts of Berths 32, 33 and 34 South Wharf. The site is located within the local government of Melbourne City Council, and within the Port of Melbourne jurisdiction.
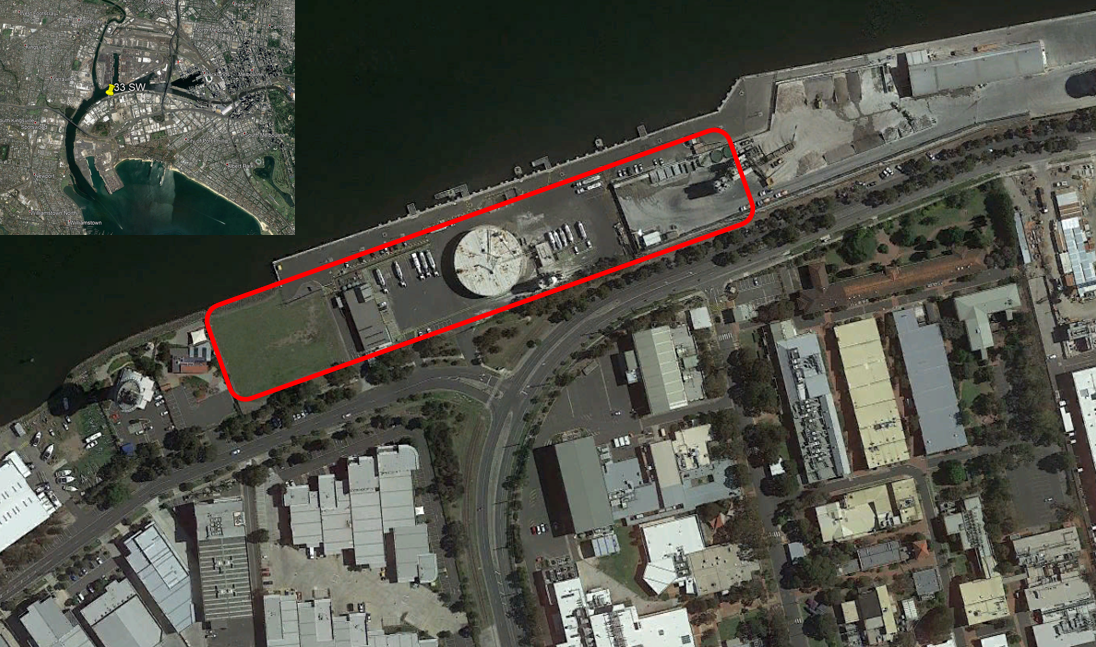
Cement Australia commenced operations at the site circa 1991 for the import, storage and despatch of flyash. In 2008 the fly ash operation was transferred to Melbourne Cement Facilities (MCF) located at 750 Lorimer Street.
The site is currently used to store and despatch speciality cements through existing silos and weighbridge as well as for the parking and maintaining of CA’s cement tanker fleet. The site is operated on a 7 day per week, 24hr per day basis.
It is proposed to construct and operate a facility that will produce Ground Granulated Blast Furnace Slag (GGBFS). This will entail constructing and operating the following major components:
- An enclosed Granulated Blast Furnace Slag (GBFS) Storage Shed
- A Vertical Roller Mill for grinding GBFS into GGBFS
- A finished product silo and weighbridges
- Upgrades to the existing facilities including:
- Wharf for unloading the GBFS
- Office and Amenities.
- Truck and vehicle parking.
The proposed activities at the site will continue to operate 7 days a week, 24 hours per day. The below Figure 2 is an artist’s impression of what the finished facility will look like.
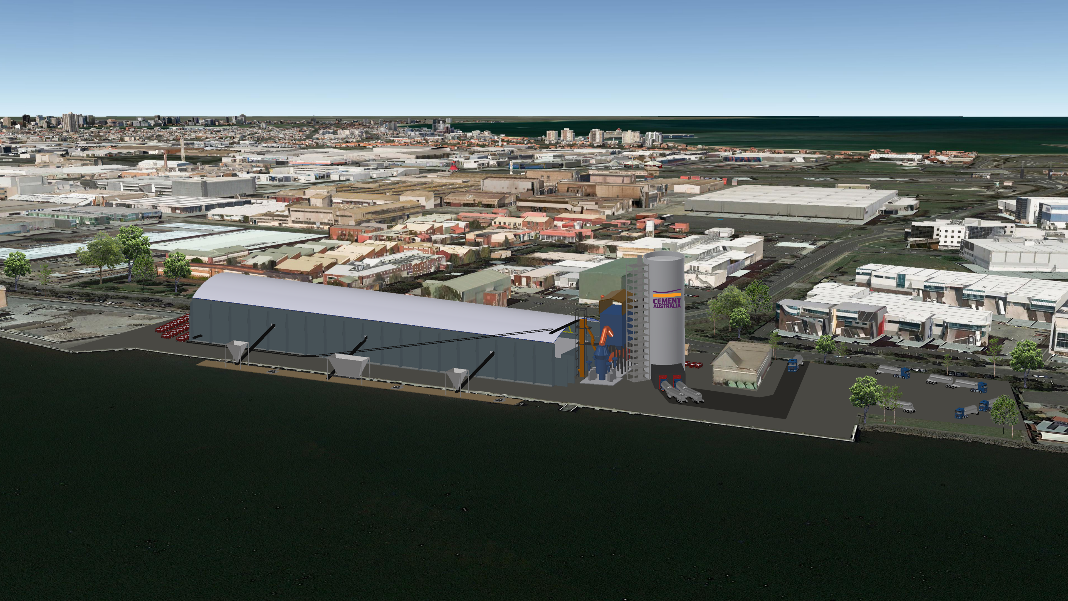
Granulated Blast Furnace Slag (GBFS) is a by-product from blast furnaces used to make iron. GBFS is then dried and ground to a fine powder called Ground Granulated Blast Surface Slag (GGBFS) which is used in the making of concrete.
GGBFS is also a key low carbon ingredient in the production of low carbon concrete.
As Melbourne and Victoria’s economy grows, increased supplies of GGBFS are vital to support construction and infrastructure projects. The proposal will help secure Melbourne’s future cementitious product supply, while supporting Victorian and Australian jobs and their economies.
Once the grinding facility is commissioned, there will be a change in the following activities:
Increase in ship movements at Berth 33
Presently the Port of Melbourne uses the current berth as a layup area for servicing ships. This activity will continue, with upgrades to the wharf area to enable unloading of the GBFS. These upgrades will be conducted as part of the mill construction.
In order to deliver the maximum production throughput of up to 400,000 tonnes of GBFS per annum, the facility will receive up to 12-13 shipments per year. Each shipment would be approximately 33,000 tonnes. Cement Australia will work with the Harbour Master to ensure compliance to the requisite maritime safety and navigation requirements.
Increase in truck movements
There are currently up to 80 truck movements per day from the facility, with the majority of truck movements occurring between Monday to Friday (peak times) and Saturdays. Following completion of the new facility, the movements will increase to a maximum of 140 truck movements per day. Based on 2015 traffic data (pre COVID-19 downturn) for Lorimer Street, this represents an increase of ~0.4% in total vehicle movements and a 5% increase on heavy vehicle volumes along Lorimer Street. Truck routes will not change.
Air emissions
The potential air emissions to be considered from an operational Slag Grinding Facility are dust, Nitrous Oxides (NOx) and Sulphur Oxides (SOx). The proposed Slag Grinding Facility will be installed with the latest technology designed to minimise all of these potential emissions.
GBFS is a granular coarse sand like material, with a relatively high moisture content. Once unloaded from the ship via ship’s grabs, the GBFS will be transported on covered conveyors into a fully enclosed storage shed. Dust generation is not expected from these activities. The GBFS is reclaimed from the storage shed and processed through the grinding mill to create GGBFS. As GGBFS has the potential for dust emissions the grinding mill will be operated under negative pressure and is also fitted with a baghouse to prevent dust emissions. Dust collectors will also be installed on other equipment used to convey the GGBFS to the silos.
Cement Australia is undertaking an air emission assessment as part of the Works Approval process, to ensure compliance with the Environmental Protection Authority (EPA) requirements
Noise
It is expected that the operation of the grinding mill will contribute to additional noise being generated at the site compared with present day. Cement Australia have engaged an external consultant to undertake a noise assessment study. Additionally, Cement Australia will work with its suppliers to ensure that equipment specifications meet prescribed noise limits at the boundary that will comply with EPA requirements.
Cement Australia is undertaking consultation with relevant stakeholders, as part of the Works Approval Application process. The feedback received during this process will help inform the proposal prior to it being lodged with the Victorian EPA.
Once the proposal is submitted with EPA, it will be placed on public exhibition by EPA for further consultation.
Find out more and have your say
Cement Australia has now submitted the application for the proposed Slag Grinding Facility, to the Environment Protection Authority (EPA) Victoria. The application and supporting documentation is available under the EPAs website by following this link - Cement Australia Pty Ltd.
If you have any questions or comments, please contact us at @email